Injection Moulding Manufacturing: Boosting Efficiency and Precision
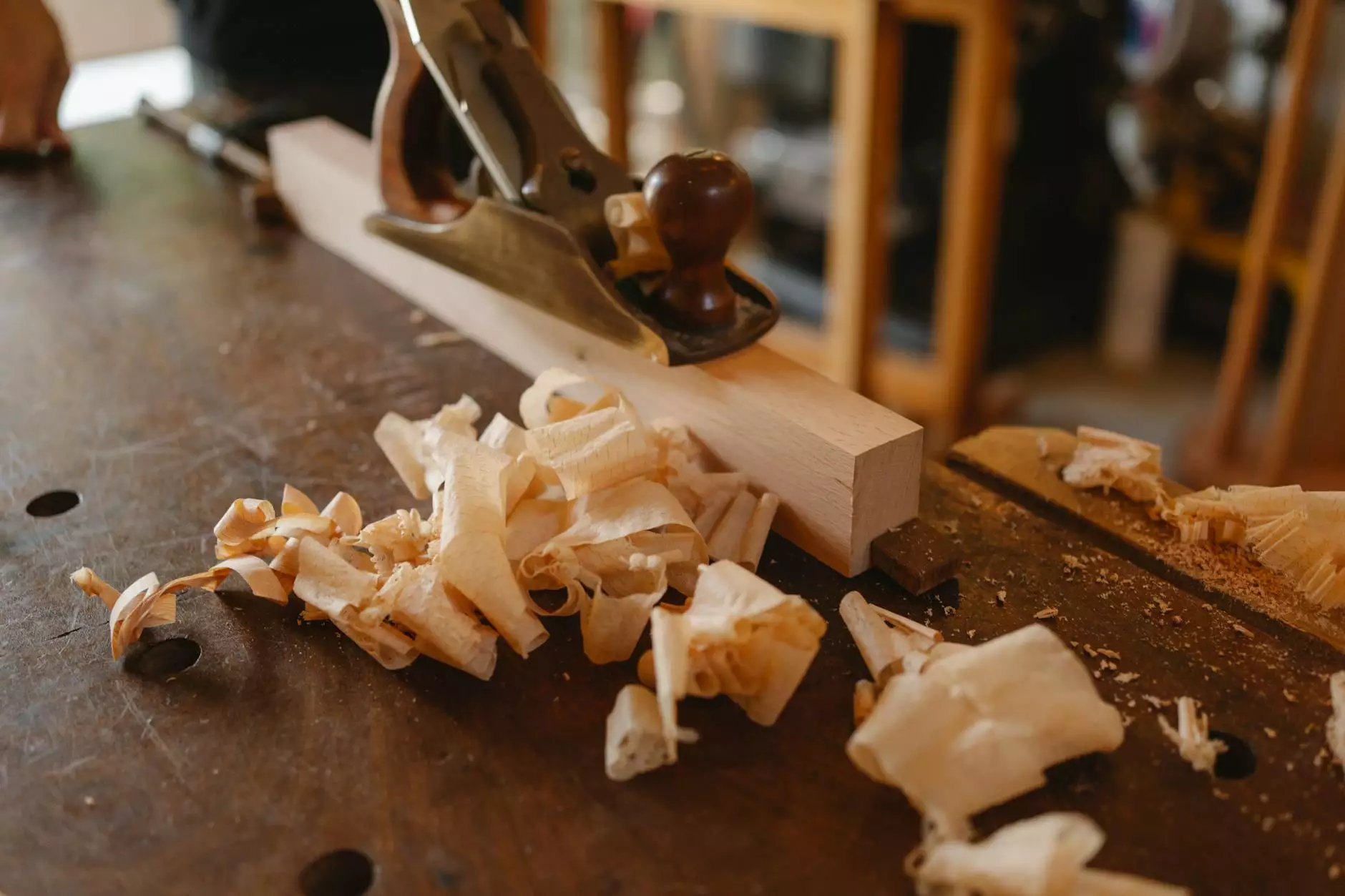
Introduction
Welcome to Deep Mould, your trusted partner in injection moulding manufacturing. We specialize in providing high-quality solutions for metal fabricators, revolutionizing the plastic manufacturing industry with our state-of-the-art injection moulding techniques. In this comprehensive guide, we will delve into the world of injection moulding manufacturing, discussing its processes, materials, machinery, and the impact it has on various industries.
The Injection Moulding Process
Injection moulding is an innovative manufacturing process that involves injecting molten plastic material into a mould to create a desired shape. This versatile process offers numerous advantages, including high efficiency, repeatable precision, and the ability to manufacture complex geometries.
At Deep Mould, we employ cutting-edge injection moulding machines to ensure optimal results. These machines consist of a hopper, heating and melting unit, injection unit, and clamping mechanism. Our skilled technicians carefully calibrate and optimize the process parameters, such as temperature, pressure, and speed, to achieve the highest quality and production efficiency.
Materials in Injection Moulding
One of the key components of injection moulding manufacturing is the materials used. Plastics or polymers in the form of pellets or granules are melted and injected into the mould cavity. Deep Mould offers a wide range of materials to suit diverse application requirements, including ABS, polypropylene, polystyrene, and nylon.
Each material offers distinct properties, such as strength, flexibility, heat resistance, and chemical resistance. Our expert team can guide you in selecting the most suitable material for your project, ensuring optimum performance and durability of the end product.
The Mould and Mould Design
The mould is a crucial component in the injection moulding process. It is a hollow cavity or form that shapes the molten plastic material and determines the final product design. Deep Mould's experienced designers utilize advanced CAD/CAM software to create precise mould designs, ensuring accurate replication of the desired shape.
Our team pays meticulous attention to detail, considering factors such as parting lines, gate location, ejection system, and cooling channels. By incorporating innovative cooling systems, we shorten the cycle time and enhance productivity while maintaining optimal part quality.
Injection Moulding Machine and Components
To achieve the highest standards in injection moulding manufacturing, Deep Mould utilizes state-of-the-art injection moulding machines. These machines are equipped with advanced technologies and features to enhance efficiency, precision, and productivity.
The injection unit of the machine carefully controls the flow and pressure of the molten plastic material, ensuring consistent fill and minimizing defects. The clamping mechanism securely holds the mould in place during the injection process, preventing any potential leaks or deformations.
Ejector pins are employed to gently push the final product out of the mould after it has solidified. At Deep Mould, we prioritize product integrity and utilize high-quality ejector pins that ensure a clean demoulding process without affecting the product's dimensions.
End-to-End Solutions for Metal Fabricators
Deep Mould caters to the diverse needs of metal fabricators, offering end-to-end solutions in injection moulding manufacturing. Our comprehensive services include design consultation, mould prototyping, mass production, quality inspection, and timely delivery.
We understand the importance of precision and reliability in the metal fabrication industry. That is why we apply stringent quality control checks at every stage of the manufacturing process. Our dedicated team conducts thorough inspections to ensure that the final product meets the highest industry standards.
Advantages of Injection Moulding Manufacturing
Injection moulding manufacturing offers numerous advantages over traditional manufacturing methods, making it a preferred choice for many industries. Some key benefits include:
- High Efficiency: With efficient cycle times and automated processes, injection moulding can rapidly produce large quantities of high-quality products.
- Precision and Consistency: The injection moulding process ensures consistent part dimensions and precise replication of intricate designs, delivering uniformity across production runs.
- Design Flexibility: Injection moulding allows the creation of complex geometries, incorporating features such as undercuts, thin walls, and intricate textures.
- Cost-Effective Production: The ability to rapidly produce large quantities with minimal waste makes injection moulding a cost-effective option for manufacturers.
- Material Versatility: A wide range of materials can be utilized in injection moulding, allowing manufacturers to select the most suitable material for their specific application.
- Sustainable Manufacturing: Injection moulding generates minimal waste, as unused plastic material can be recycled, contributing to a more sustainable manufacturing process.
The Impact of Injection Moulding Manufacturing
Injection moulding manufacturing plays a crucial role in various industries, enabling the production of diverse products that improve our daily lives. From aerospace and automotive to medical devices and consumer goods, plastic components manufactured through injection moulding are integral to countless modern applications.
Deep Mould has a rich history of partnering with companies across a wide range of sectors, contributing to advancements in the products they bring to market. Our commitment to innovation, quality, and customer satisfaction has positioned us as a market leader in injection moulding manufacturing.
Conclusion
Injection moulding manufacturing is a highly efficient and precise process that revolutionizes the manufacturing industry. At Deep Mould, we take pride in providing top-notch solutions for metal fabricators, utilizing state-of-the-art machinery, high-quality materials, and expert craftsmanship to deliver superior results. Partner with us to unlock endless possibilities in injection moulding manufacturing and drive your business to new heights.